Low lifetime cost RBC wastewater treatment plant for total nitrogen and phosphorous (nutrient) removal
KEE Process was commissioned to develop municipal wastewater treatment plants and include features to ensure that the plants are designed to operate during the high summer and low winter loads without losing performance, provide low lifetime cost, low capital cost, low energy cost, low day to day operational input and low sludge production rates.
Over the last few years, KEE has provided solutions for total nutrient removal for small, medium and large scale systems and these systems have been type tested by various authorities. There is a requirement for many locations in the sun-kissed Mediterranean that systems are capable of operating during the high summer usage and low winter usage, whilst maintaining the plant performance. In addition to this, the plant must be able to operate without the need for daily or weekly operational input. KEE was required to produce two such systems, one for Southern Spain and one for Northern Spain. Both sites required operation in fluctuating summer and winter conditions.
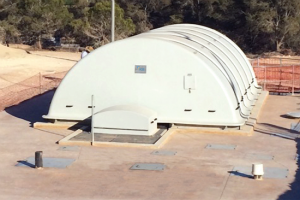
KEE 4.5m Diameter RBC – with built in flow attenuation system for plant process optimisation.
Site 1 in Southern Spain (warm sub-tropical climate) The plant in Southern Spain is a site that includes holiday chalets, a golf club, recreation clubs, restaurants and bars. The first phase of the plant had to operate for 10% of the ultimate design load, as the facilities were under construction but, as the facilities were gradually built and occupied, the plant had to keep up with the gradual increase in flows and loads whilst maintaining process performance. In addition, it was also a requirement that the plant was of a modular construction to phase the build programme to spread the capital cost. The first phase module had to be designed to treat 300m3/d of municipal wastewater but also had to cope with gradual increase in load.
The first phase module was required to treat:
- 300 m3/d,
- BOD 440 mg/l
- NH4-N 74mg/l
- TKN 80 mg/l.
The final discharge consent:
- SS < 35 mg/l
- BOD < 25 mg/l
- COD < 125 mg/l
- TN < 25 mg/l
- NO3-N < 13 mg/l
- PTOT < 2 mg/l
The plant proposed and supplied by KEE included prefabricated Glass-fibre Reinforced Polyester (GRP) Primary Settlement Tanks which provide the facility to separate gross solids as sludge, flow attenuation and sludge storage. This was followed by one 4.5m diameter, five-bank RBC, installed in an in-situ concrete tank. KEE RBCs include a patented flow-management system which provides a flow and load attenuation system for process performance optimisation and also creates the necessary conditions for nitrification – denitrification within the RBC.
The whole RBC is covered with lightweight GRP sectional covers. The RBC was fitted with an automated and fully flexible internal recycle system to manage the nitrification de-nitrification requirement of the plant.
For separation of biological solids generated in the RBC, the system includes a prefabricated hopper bottom GRP radial upward flow settlement tank with effective tank surface area of 19.2m2. The final settlement tank includes a fully automated pump-assisted hydrostatic sludge and scum draw-off system to periodically remove and return the scum and sludge to the head of the PST for co-settlement with primary sludge.
The plant components were built off-site in the UK and delivered, all ready for final assembly on site. KEE built the whole plant and all the internal pipe-work on-site in four weeks and was ready to receive flows shortly after that.
This newly built RBC plant covers an initial build phase on-site. The full development proposed increases over the next few years which will result in 10 systems of this size being built and installed at various times over an agreed time period. The energy consumption for the plant for the current low flow of 200 m3/d is 88 kWh/d. This is projected to be 115kWh/d when the flow reaches the designed high season flow of 300 m3/d.
Spot sample result five weeks after initial process commissioning flow rate of 200 m3/d.
INLET OUTLET
mg/l mg/l
BOD 440 24.0
COD 716 79.0
NH4-N 92 5.2
TN 98.8 19.2
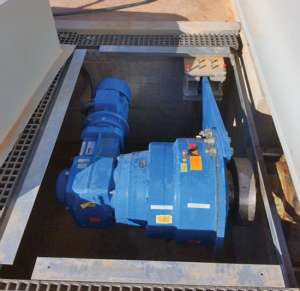
KEE 4.5m Diameter RBC – drive system.
Site 2 in Northern Spain (Temperate Climate)
The plant in Northern Spain was for a smaller population in a village of 170 PE initially, but the local authorities required that the plant should be capable of treating the future projected load from 400PE. The important features to be included in the design were that the same plant should be designed to comply with the performance for both the current load and future projected load whilst maintaining the minimal operations cost and sludge management cost.
The design criteria for the plant in Northern Spain were:
- 17 m3/d for current PE of 170 & 40 m3/d for the future projected PE of 400
- BOD 600 mg/l
- NH4-N 75 mg/l
- TKN 81 mg/l.
The final effluent discharge consent:
- SS < 35 mg/l
- BOD < 25 mg/l
- COD < 125 mg/l
- TN < 15 mg/l
The plant for this smaller contributory PE was designed and built along similar lines as the Phase 1 module for Southern Spain and all the equipment was totally factory built, including the RBC which was housed in a GRP tank and also covered with lightweight sectional GRP covers.
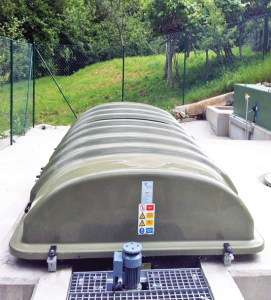
KEE 2.35m Diameter RBC unit – on site installation and ready for receiving flows.
KEE supplied a 2.35m diameter RBC, fitted with patented managed flow system for flow and load attenuation, internal recycle, automated pump assisted hydrostatic FST sludge and scum removal system, together with built-in flexibility to readily adapt the plant for such a large fluctuation in flows and loads, whilst maintaining full compliance with effluent discharge criteria including full nitrification and de-nitrification.
The plant was commissioned in April 2014 and the performance of the plant is significantly beyond the design expectation. The energy consumption of the RBC is 15kWh/d for the current load and is projected to be 35kWh/d for the future PE of 400.
Results for the 28 days test period on 95 percentile basis is detailed below for a flow rate of 17.8 m3/d.
INLET OUTLET
mg/l mg/l
BOD 854 9.1
COD 1,708 62.0
SS 518 13.0
NH4-N 126 1.3
TKN 135 12.1
For both the sites, KEE also included a feature within the plant design to aerobically digest the sludge during low load periods to (a) reduce sludge management costs and (b) to keep the plant fully operational biologically and ready for the onset of the full load period.
The benefits for the client are that the ownership costs are reduced, the carbon footprint is reduced by avoiding long sludge tanker journeys and the plant is maintained in readiness for the increase in flows and loads of the peak period.
Author: Suru Nathwani B.Eng (Chem), Group MD of KEE
To see the capabilities of the KEE Group of companies please visit the KEE Group website.
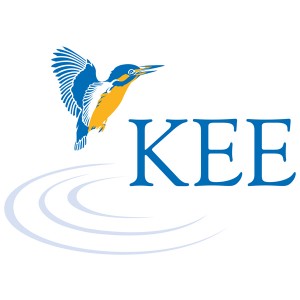
